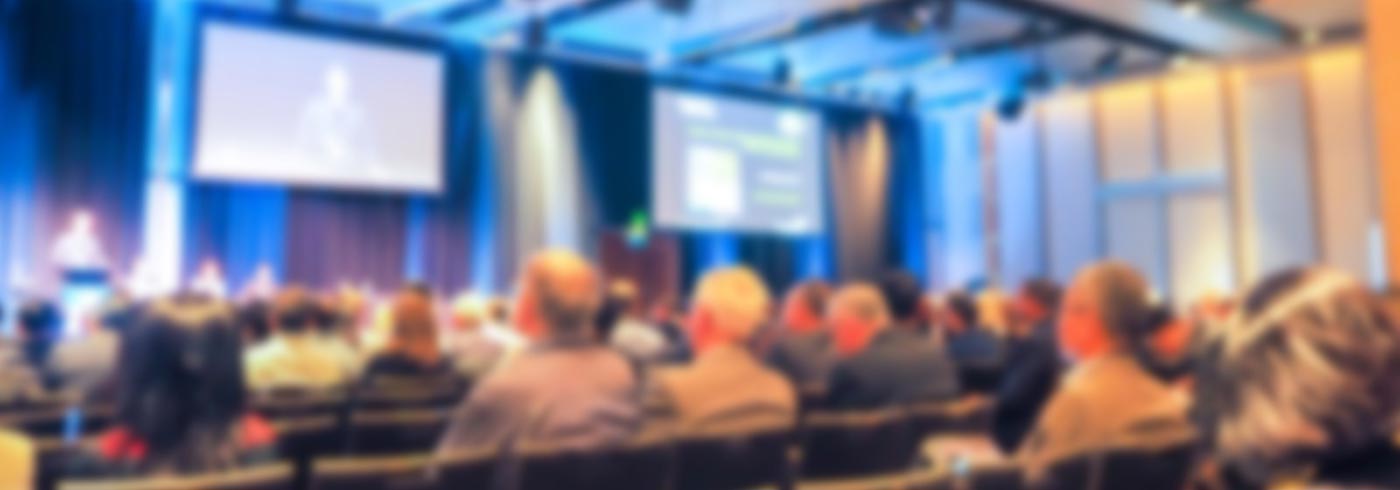
INFORMATION TEXT ON PREVENTION OF MAJOR INDUSTRIAL ACCIDENTS POLICY (PMIAP)
1. PURPOSE
This document is prepared to inform relevant parties (public/government units, visitors, etc.) about measures and precautions implemented by ZSR Patlayıcı Sanayi A.Ş. during its activities for prevention of any potential industrial accidents.
2. SCOPE
This document covers the activities and processes involving any hazardous materials as listed in Annex-1 of Regulation on Preventing and Reducing the Effects of Major Industrial Accidents as published in the Official Journal No: 30702 dated 02.03.2019 that are used and/or stored by ZSR Patlayıcı Sanayi A.Ş. and/or are a part of its operations.
3. DEFINITIONS AND DESCRIPTIONS
SC: means Safety Report
Establishment: means ZSR Patlayıcı Sanayi A.Ş.
Regulation: means Regulation on Preventing and Reducing the Effects of Major Industrial Accidents
4. PUBLIC DISCLOSURE ON SAFETY REPORT ACTIVITIES
4.1. Establishment’s Name and Full Address:
Establishment’s registered business name as it appears in its certificate of activity is ZSR Patlayıcı Sanayi A.Ş., and the establishment carries out its activities at Kavaklı Mah. Kavaklı Sok. No: 1B 10100 Karesi/Balıkesir.
4.2. Establishment’s Regulatory Scope
In accordance with the requirements of Article 7 of the Regulation on Preventing and Reducing the Effects of Major Industrial Accidents, ZSR Patlayıcı Sanayi A.Ş. has filed relevant statements through communication system of the Ministry of Environment and Urbanization (see Annex-1 for Official Notice), and has been designated as a high-level establishment. As per its scope, the establishment is subject to said regulation, and has prepared and filed the “Safety Report” as required under Article 11.
4.3. Summary Information about Establishment’s Activitiess
Establishment has a facility of 468924 square meters, of which the indoor space measures 18713 square meters. Establishment manufactures booster-sensitive emulsion explosives, cap-sensitive emulsion explosives, ANFO, shotgun shells, blank sound cartridges, plastic plugs, 9x19 mm, 5.56x45 mm, 7.62x39 mm, 7.62x51 mm, 7.62x54 mm, 12.7x99 mm, 12.7x108 mm cartridges and various types of bullets, as well as boxer primers and chemical mixtures. Processes approaches are as summarized below.
Manufacturing of Shotgun Shells: Shotgun shells are manufactured in accordance with C.I.P. standards by fully automatic machines capable of precision filling. Primed cases, pellets, and plastic plugs are loaded into vessels of machines that are located in a separate area. In addition, there are air conditioning rooms for each machine where automatic powder feeding is performed. Machine carries out assembly operation by conveying primed cases, powder, plugs, and pellets into the feeding chambers respectively. Machine checks the powder and pellet weight by means of electronic controllers available on it. Assembled shells are subjected to test fires by ballistic test device, and then subjected to marking and packaging operations upon satisfaction of required quality criteria.
Manufacturing of Black Sound Cartridges; Blank sound cartridges manufactured in accordance with C.I.P. standards by fully automatic machines capable of precision filling. Primed case, powder, and plastic plug are assembled automatically by the machine. Powder weight is checked by means of electronic controllers available on the machine. Assembles cartridges are subjected to functioning and ballistic fires, ensuring compliance with the required quality criteria.
Manufacturing of 9x19 mm Cartridges9mm cartridges are a combination of case, powder, and bullet. At first stage, case cups are forged into cases by cold forming by multi-station eccentric presses. Cases manufactured by presses are then subject to normalization (stress relieving) treatment. Then they are subject to grooving and cut-to-length treatments, and checked in terms of both size and appearance using image processing technology with electronically controlled machines. Finally, they are ready for primer assembly. At second stage, jacket cups are forged together with bullet core by assembly presses to produce bullet.
At final stage, primed cases are combined with powder and bullet by automatic assembly machines, and turned into cartridges. Powder weight, length, and form are checked by electronic and mechanical controllers available on the machine. In ballistic test laboratory, cartridges are subject to essential ammunition tests (strike sensitivity, electronic pressure and velocity measurement, powder and primer compatibility, primer sensitivity, tightness, functioning and safety, pull and hardness measurement, bullet trajectory accuracy, extreme weather conditions (+52°C / -54°C)), ensuring manufacturing according to applicable standards (EPVAT, SAAMI, CIP, NATO).
Manufacturing of 5.56x45 mm, 7.62x39 mm, 7.62x51mm, 7.62x54 mm 12.7x99 mm ve 12.7x108 mm Cartridges :Manufacturing of cartridges is carried out in accordance with military and civilian use requirements by fully automatic machines capable of precision filling. Machine automatically assembles the primed case, powder, and bullet; and checks powder weight, length, and form by means of electronic and mechanical controllers available on it. In ballistic test laboratory, cartridges are subject to essential ammunition tests (strike sensitivity, electronic pressure and velocity measurement, powder and primer compatibility, primer sensitivity, tightness, functioning and safety, pull and hardness measurement, dispersion, terminal effect, trace performance, extreme weather conditions (+52°C / -54°C)), ensuring manufacturing according to applicable standards (EPVAT, SAAMI, CIP, NATO).
Manufacturing of Boxer Primers :Primer is a combination of cup, anvil, and chemical mixture. Cup and anvil are manufactured by eccentric presses using progressive and cutting moulds. Mixture conveyed by a carrier vessel specially designed for the assembly line is combined with cup and anvil to make a primer. All manufactured primers are checked by electronically controlled size inspection machine, and then subjected to sensitivity test. The process proceeds with packing and packaging operations upon satisfaction of required quality standards.
Manufacturing of Cap-sensitive Emulsion Explosives:These are water-resistant explosives manufactured by mixing ammonium nitrate, emulsion, and sensitivity enhancing solution. For manufacturing the emulsion, the oxidizer solution prepared with ammonium nitrate, oxidising salt, and water is mixed with oil and wax at high speed. Emulsion and ammonium nitrate are mixed by horizontal mixer, and conveyed to product bunker. Then the mixture is pumped into the cartridge feeder. Subsequently, the mixture is further mixed with sensitivity enhancing solution in a mixer, and then filled into polymeric film cartridges of desired diameters and lengths, which cartridges are then secured with clips. Cartridges are subject to cooling process, and then placed into cardboard boxes which are then stacked on pallets in pre-designated stacking order, and are stored in warehouse. Traceability of all cartridges, boxes, and product pallets is ensured through QR codes printed on them using a barcoding system. During manufacturing, samples are taken at designated intervals to ensure that density value of the mixture is regularly checked. Thus, the product quality is ensured to be within standard quality range. Cap-sensitive explosives are detonated by a cap used as a trigger.
Manufacturing of Booster-sensitive Emulsion Explosives (Heavy ANFO): These are water-resistant explosives manufactured by mixing ammonium nitrate, fuel oil, emulsion, and micro glass bubbles. For manufacturing the emulsion, oxidizer solution prepared with ammonium nitrate and water is mixed with oil mixture at designated ratios. The manufactured emulsion, a semi-finished product, is then filled into stock tanks. When the ammonium nitrate in the bunker is conveyed through the helical system by means of auger, fuel oil is dosed into the auger by means of fuel oil dosing lines which are connected to the auger, which as a result ensures a homogenous mixture. The resulting homogenous mixture is conveyed into helical mixer where it is mixed with emulsion and micro glass bubbles with the aid of the dosing lines connected to the mixer. The mixture which is turned into a product as detailed above is then conveyed into cartridge feeder where it is filled into polymeric film cartridges of desired diameters and lengths, which cartridges are then secured with clips. Booster-sensitive emulsion explosive in the cartridge is placed into cardboard boxes which are then stacked on pallets in pre-designated stacking order, and are stored in warehouse. Traceability of all cartridges, boxes, and product pallets is ensured through QR codes printed on them using a barcoding system. During manufacturing, samples are taken at designated intervals to ensure that density value of the mixture is regularly checked. Thus, the product quality is ensured to be within standard quality range. Booster-sensitive explosives are detonated by cap-sensitive emulsion explosives which are used as a trigger.
ANFO Manufacturing : ANFO is a prill porous ammonium nitrate and fuel oil mixture. Unlike emulsion explosives, ANFO is not water resistant. In ANFO manufacturing, first, the ammonium nitrate in big-bags is carried by means of a crane, and discharged into nitrate filling bunker. When the ammonium nitrate in the bunker is conveyed through the helical system by means of auger, fuel oil is dosed into the auger by means of fuel oil dosing lines which are connected to the auger, which as a result ensures a homogenous mixture. The ammonium nitrate and fuel oil mixture which comes out of the auger in a homogenous form is conveyed to product bunker. The mixture conveyed into bunker through the filling machine is then weighed and filled into liquid-tight 25-kg layered bags. Finally, the mouth of bags is sewn by a sewing machine. ANFO bags which are ready for shipping after sewing process are stacked on pallets, and then stored in warehouse. Traceability is ensured through QR codes printed all bags and product pallets using a barcoding system. During manufacturing, the fuel oil percentage of the mixture is checked by means of a flow meter and sampling at regular intervals. Thus, the product quality is ensured to be within standard quality range. ANFO explosives are detonated by cap-sensitive emulsion explosives which are used as a trigger.
Manufacturing of Non-electric Detonators: The final product which is a combination of custom-made shock tubes and blasting caps with different delay periods is named as non-electric detonator. There are different combinations depending on different areas of use such as underground and aboveground. Combinations are determined according to delay periods of detonators. Depending on the intended use, red clips, colour surface blocks are used as auxiliary equipments. During assembly, first the shock tubes are cut to desired length, and then fixed. Then one of the ends of the shock tube is welded and a product label is applied. The other end of the shock tube is fixed to blasting caps with a tight rubber plug, and then secured with clips. Traceability of packaged products is ensured through QR code printed by means of a barcoding system.
4.4. Basic Hazard Statements for Hazardous Substances which may Cause a Major Accident
Name of Hazardous Substance | Basic Hazard Code and Explanation |
---|---|
Ammonium Nitrate | H272: May intensify fire; oxidizer. H319: Causes serious eye irritation. |
Anfo (Type B) | H201: Explosive; mass explosive hazard. H319: Causes serious eye irritation. H351: Suspected of causing cancer. |
Sodium Nitrite | H272: May intensify fire; oxidizer. H301: Toxic if swallowed. H319: Causes serious eye irritation. H400 Very toxic to aquatic life. H350 May cause cancer. |
Fuel Oil | H226: Flammable liquid and vapour. H304: May be fatal if swallowed and enters airways. H315: Causes skin irritation. H332: Harmful if inhaled. H351: Suspected of causing cancer. H373: May cause damage to organs through prolonged or repeated exposure. H411: Toxic to aquatic life with long-lasting effects. EUH066: Repeated exposure may cause skin dryness or cracking. |
Antimony Trisulfide | H302: Harmful if swallowed. H332: Harmful if inhaled. H400: Very toxic to aquatic life. |
Acetic Acid | H226: Flammable liquid and vapour. H314: Causes severe skin burns and eye damage. |
Sodium Perchlorate | H271: May cause fire or explosion; strong oxidizer. H302: Harmful if swallowed. |
Nitric Acid | H272: May intensify fire; oxidizer. H314: Causes severe skin burns and eye damage. H331: Toxic if inhaled. EUH071: Corrosive to respiratory tract. |
Heavy Anfo(Type E) | H203: Explosive; fire, blast or projection hazard. H351: Suspected of causing cancer. H319: Causes serious eye irritation. H335: May cause respiratory irritation. H315: Causes skin irritation. |
Sulphuric Acid | H290: May be corrosive to metals. H314: Causes severe skin burns and eye damage. |
Nitrocellulose | H228: Flammable solid. H319: Causes serious eye irritation. H336: Causes drowsiness or dizziness. |
Powder | H203: Explosive; fire, blast or projection hazard. H373: May cause damage to organs through prolonged or repeated exposure. H300: Fatal if swallowed. H310: Fatal in contact with skin. H330: Fatal if inhaled. H411: Toxic to aquatic life with long-lasting effects. |
Ammonium Nitrate Solution | H315: Causes skin irritation. H319: Causes serious eye irritation. |
LPG | H220: Extremely flammable gas. H280: Contains gas under pressure; may explode if heated. |
Pentaerythritol Tetranitrate | H200:Unstable explosive. H201: Explosive; mass explosion hazard. |
4.5. Information about Actions to be Taken in case of a Major Accident in the Establishment
In case a major industrial accident occurs in the establishment as a result of abovementioned hazardous substances, the emergency management procedures will be initiated according to “ZSR Patlayıcı A.Ş. Emergency Action Plan” which is then in effect.
- • Establishment has a rescue, fire fighting, protection, first aid, and emergency guidance team consisting of trained personnel having suitable equipments. In case a major accident occurs, that unit and team will go to the scene of incident, ensure safety of the scene of incident, and implement suitable response method(s) based on the type of hazardous substances avoiding any possible risks.
- • Following an emergency alarm, relevant emergency-response actions will be taken at the scene of incident and, in the meantime, the switchboard operator or security unit will in accordance with Emergency Communications Procedure inform the workplace officers, and call relevant municipality and/or metropolitan municipality fire department, emergency services, and law enforcement departments (Ambulance, Police, Gendarmerie, etc.), and give them the following information:
- Occurrence and progress of accident.
- Relevant hazardous substances and their quantities.
- Available data as required to evaluate effects of the accident on human health, environment, and property.
- Measures taken as per the emergency scenario.
- For communication purposes, name and contact details of the person in charge of handling the whole operation at establishment’s emergency management centre.
- • Person(s) authorized by the Occupational Health and Safety Manager or Emergency Management Team will simultaneously give the foregoing information to the Governorship, Provincial Directorate of Environment and Urbanization, Provincial Directorate of Disaster and Emergency, and Provincial Directorate of Health.
- • Occupational Health and Safety Manager will, within sixty days following a major accident, complete the accident report section available on the notification system, print it, and then submit the printed report to the Provincial Directorate of Environment and Urbanization and the Provincial Directorate of Disaster and Emergency. Relevant information will be updated in case any new information concerning mitigation of medium and long term effects of the accident and prevention of reoccurrence of such an accident or in case any additional findings which amend any foregoing information are obtained as a result of a further investigation.
4.6. Information about Measures for Scenarios of any Major Accident which may occur in the Establishment, and Their Potential Effects to Environment
Based on Quantitative Risk Assessment studies, ZSR Patlayıcı Sanayi A.Ş. has established scenarios for any major accidents which it may face due to its manufacturing operations, and documented under “Major Accident Scenario Forms” relevant accident scenarios including relevant safety and security measures, and control methods in case of an accident. Such accidents scenarios are classified under 3 main headings as summarized below:
- • Explosion and fire occurring in the manufacturing facilities (explosives manufacturing facilities)
- • Spill from relevant tanks of the fuel oil used for manufacturing of explosives
- • Explosion and fire which may occur in explosives storages
General measures taken in the establishment in order to avoid abovementioned accident scenarios are as follows:
Organizational Preventive Measures: Instructions have been prepared relating to use of machines and measures to be taken in the facility in case of any emergencies. Such instructions have been posted at relevant places, and notified to relevant personnel. Suitability of instructions is tested through drills. Criminal records of staff members employed in particular in sections subject to risk of major industrial accidents are checked, and such staff members are, prior to their assignment, duly informed about any measures required to be taken in case of any risks, and the importance of preventive actions, etc. A staff member will not be allowed to work alone upon assignment. First, the staff member is assessed from various aspects including his/her technical knowledge, communication with other staff members, and stress management abilities. In case a staff member is found to display lack of concentration and focus, proneness to violence, or short temper, relevant actions will be taken immediately. Technical Preventive Actions: When a new machine is to be bought for the facility, we receive information about the machine to be bought including information about its technical adequacy and protective measures against any possible accidents. Though the manufactured products are hazardous substances, they alone have no combustion or explosion risk. The manufactured products pose explosion risk under pressure or when triggered by a detonator/cap, etc. Therefore, relevant measures have been taken as defined under risk assessment study to ensure that there are no sources of ignition in the places of manufacturing and storage of the semi-finished or finished products (no electrical connections in storage areas of explosives; use of electrical systems with no spark and arc discharge in the facilities where manufacturing of explosives is carried out; having in place sufficient fire extinguishing systems suitable for the relevant substances and materials, etc.) Alarm systems are activated in case of any failure with the sensors used in process systems (such as production line tank, pump, etc.). According to provisions of the “Regulation on Manufacturing, Import, Transportation, Conservation, Storage, Sale, Use, Disposal, and Inspection Rules and Principles for Unmonopolized Explosives, Hunting Materials and Alike”, facilities are located at a certain distance from other facilities, and there are hills between the factory and settlements.
It is predicted that in case of any fire or explosion which would occur in spite of any measures taken within the establishment, humans and environment may face certain consequences such as vapour cloud explosion, toxic cloud, thermal radiation, high pressure, and toxic effects. However, the accident frequency calculations carried out within the establishment showed that the probability of damage is, with the effect of safety barrier which is being implemented and recommended, below the major industrial accident frequency limit value as defined under applicable regulation.
4.7. Information about Mitigation of Effects of a Major Accident which may Occur in the Establishment
ZSR Patlayıcı Sanayi A.Ş. has prepared and implements an Emergency Action Plan to handle and minimize effects of any major industrial accident. Establishment’s Emergency Action Plan provides a detailed explanation of prevention, evacuation, rescue, damage reduction methods and evacuation-shelter plans, including communication with emergency services units, for each individual case which poses a hazard beyond ordinary circumstances. To ensure preparedness for the designated scenarios, implemented measures are monitored through annual drills, and records of such drills are kept. This approach ensures safety of the establishment itself and its environment.
4.8. Information about Cooperation with Emergency Services Units in case of a Major Accident in the Establishment
ZSR Patlayıcı Sanayi A.Ş. is not located in an Organized Industrial Zone or Industrial Zone. Therefore, in case of any potential major industrial accident which may occur in the facility, the crisis will be managed in cooperation with Emergency Services Units and Provincial Directorates of Disaster and Emergency. In case any major industrial accident occurs in the establishment, the following information will be provided to emergency services units and Provincial Directorates of Disaster and Emergency:
- • Company name and address
- • Place and time of incident
- • Section/department where the accident occurred (storage areas, explosives facilities, ammunitions facilities, etc.)
- • Type of accident (fire, explosion, chemical leak, toxic emission, radioactive emission, etc.)
- • Equipment(s) subject to accident (tank, pipe, steam boiler, silo, etc.)
- • Hazardous substance available in the equipment
Response teams consisting of company personnel trained and specially equipped to respond to any incidents within the establishment will be under control and act in accordance with the directions of the relevant competent external team upon arrival of such team. Within sixty days following occurrence of a major accident in the establishment, the accident report section available on the notification system will be completed, printed, and then submitted to the Provincial Directorate of Environment and Urbanization and the Provincial Directorate of Disaster and Emergency.